Introduction
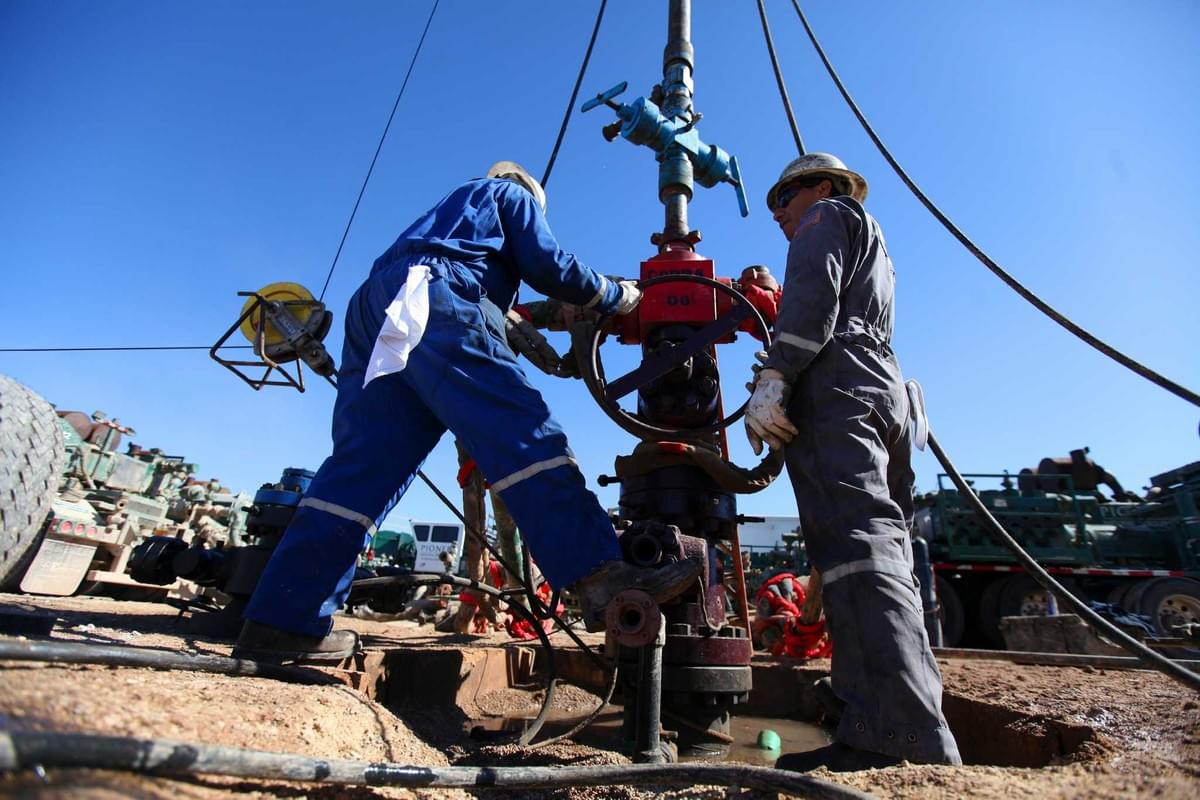
Deep hole drilling tools are essential for creating precise and accurate holes in various materials. Whether it's for saw holes, drilling cores, or any other application, having the right drill and accessories is crucial for achieving optimal results. When selecting the best boring tools, it's important to consider factors such as durability, precision, and efficiency to ensure maximum performance.
The Importance of Deep Hole Drilling Tools
Deep hole drilling requires specialized equipment to achieve clean, precise holes efficiently. Here are the key reasons why deep hole drilling tools are essential:
- Superior Accuracy and Clean Holes: Deep hole drilling tools are designed to maintain stability and precision throughout the drilling process, resulting in clean and accurate holes with minimal deviation.
- Reduced Effort and Downtime: Compared to conventional drilling methods, deep hole drilling tools minimize operator effort and drilling time, leading to increased efficiency and reduced downtime.
- Critical for Key Industries: Deep hole drilling is vital in industries like aerospace, automotive, and oil and gas, where structural integrity and precise hole placement are crucial. These tools ensure the creation of holes that meet demanding specifications.
- Improved Efficiency and Reduced Errors: Selecting the right deep hole drilling tool for the job optimizes the process, minimizes errors, and saves time and resources.
By utilizing the proper deep hole drilling tools, operators can achieve superior results, enhance efficiency, and ensure the structural integrity of their projects.
Key Considerations for Selecting the Best Tool
Selecting the most suitable tool for deep hole drilling requires careful evaluation of several factors. Here's a numbered list to guide your decision-making process:
- Project Requirements: Consider the type of material you'll be drilling, the desired depth, and the required level of accuracy.
- Tool Performance and Reliability: Opt for a high-performance tool that can handle deep drilling in your chosen material while delivering consistent and reliable results.
- Maintenance Needs: Evaluate the tool's maintenance requirements and how they align with your resources and expertise.
- Compatibility: Ensure the tool is compatible with your existing equipment for a smooth integration into your workflow.
By prioritizing these considerations, you can select a deep hole drilling tool that optimizes your project's efficiency, accuracy, and cost-effectiveness.
Benefits of High-performance Tools
High-performance deep hole drilling tools offer a significant edge over traditional options. These advanced tools are engineered to tackle demanding projects while delivering exceptional results. Here's how investing in high-performance drilling tools can benefit your operation:
- Enhanced Productivity and Reduced Cycle Times: These tools work faster and more efficiently, allowing you to complete projects quicker and maximize output.
- Improved Accuracy and Reduced Deviation: High-performance tools deliver precise results with minimal variation, ensuring consistent quality and reducing rework.
- Long-Term Cost Savings: While the initial investment might be higher, the durability and efficiency of these tools lead to significant cost savings over time due to fewer replacements and reduced material waste.
- Enhanced Operational Efficiency: Faster drilling times, improved accuracy, and reduced waste contribute to a smoother workflow and overall operational efficiency.
- Safer Work Environment: The consistent performance of high-performance tools minimizes errors and accidents, protecting your workforce and reducing the risk of downtime and liabilities.
By investing in high-performance deep hole drilling tools, you can achieve greater productivity, improve accuracy, and ensure a safer work environment for your employees.
Exploring the World of Deep Hole Drilling
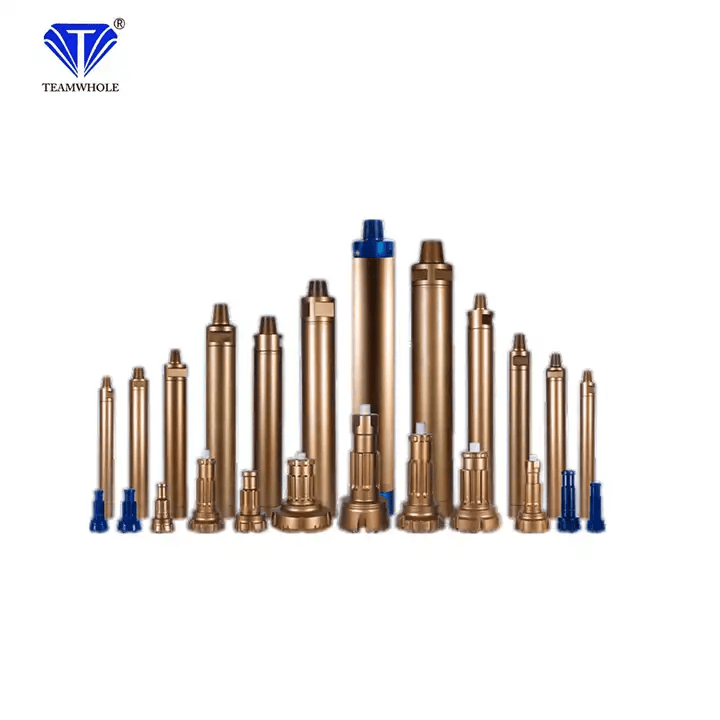
Several tools can be used for deep hole drilling. From saw holes to drilling cores, each tool serves a unique purpose in creating precise and accurate holes for various applications. The saw hole bit, for example, is designed to create smooth and clean cuts in materials such as metal or wood, while drilling tools encompass a wide range of equipment used to bore holes of varying sizes and depths.
Types of Deep Hole Drilling Tools
Deep hole drilling requires specialized equipment to create long, precise holes with minimal deviation. Here are the key types of tools used for this demanding process:
- Gundrills: These single-flute drills create deep holes (diameters typically between 1mm and 50mm) with high accuracy. They utilize high-pressure coolant to remove chips and maintain drill integrity.
- BTA Drills (Boring Trepan Annular): Designed for larger diameters (20mm to 250mm and above), BTA drills feature multiple cutting edges and an internal passage for chip removal.
- Ejector Drills: A variation of BTA drills, ejector drills use pressurized coolant to remove chips and debris from the hole efficiently.
- Cutting Fluids and Lubricants: These specially formulated fluids are essential for cooling the drill bit, lubricating the cutting process, and flushing away chips.
Choosing the right deep hole drilling tools depends on the desired hole size, material properties, and project requirements. By utilizing these specialized tools and techniques, deep hole drilling can be achieved with exceptional accuracy and efficiency.
Key Features to Look for in High-performance Tools
High-performance deep hole drilling requires specialized tools to achieve optimal efficiency and results. Here are some key features to consider when selecting your deep hole drilling tools:
- Advanced Cooling Systems: Overheating is a major concern during deep hole drilling. Look for tools with internal coolant channels or external jetting systems that effectively direct coolant to the cutting zone, preventing heat buildup and ensuring smooth chip evacuation.
- Precision Cutting Edges: Clean and accurate holes are essential for many applications. High-performance deep hole drills should feature precisely ground cutting edges that minimize deflection and vibrations, resulting in superior hole quality that may eliminate the need for additional finishing steps.
- Durable Construction Materials: Deep hole drilling can be demanding on tooling. Select tools constructed from high-strength materials like carbide or cobalt-mixed high-speed steel. These materials provide exceptional wear resistance and extended tool life, even in challenging drilling environments.
By prioritizing these key features, you can ensure your deep hole drilling operations achieve optimal performance and efficiency and produce high-quality results.
Applications and Industries that Benefit from High-performance Tools
High-performance deep hole drilling tools are essential for various applications and industries. From aerospace manufacturing to automotive production, these tools are crucial in creating intricate components with tight tolerances and complex geometries. Additionally, industries such as oil and gas exploration rely on high-performance drilling tools to extract resources deep beneath the earth's surface.
By understanding the different types of deep hole drilling tools available and the key features to look for in high-performance options, you can make informed decisions when selecting the right tool for your specific application needs.
The Top Players in the Industry
When it comes to deep hole drilling tools, Tianhe has established itself as a leading player in the industry. With a strong focus on innovation and quality, Tianhe has become a trusted name for those seeking high-performance drilling tools. Their commitment to excellence has set them apart from other manufacturers, making them a top choice for businesses and industries worldwide.
1. Tianhe's Leading Role in Deep Hole Drilling
Tianhe's expertise in deep hole drilling tools is evident in their TH–900 Hydraulic Crawler Drill Rig. This state-of-the-art equipment is designed to saw holes and drill cores with precision and efficiency. Equipped with advanced features and cutting-edge technology, this rig is a game-changer for those looking to maximize performance in their drilling operations.
The TH-900 Hydraulic Crawler Drill Rig has a powerful hydraulic system that provides the necessary force to penetrate even the toughest rock formations. This ensures that drilling operations can be carried out smoothly and efficiently without unnecessary delays or complications. The rig's robust construction and durable materials also contribute to its reliability and longevity, making it a valuable asset for any deep hole drilling project.
Features of Tianhe's TH–900 Hydraulic Crawler Drill Rig
The Tianhe TH-900 Hydraulic Crawler Drill Rig is a powerful and versatile machine designed to conquer even the most challenging drilling projects. Here are some of its key features:
- Advanced Hydraulic System: Provides precise control and smooth operation for efficient drilling, ensuring accuracy and productivity.
- Compact and Agile Design: Its design allows for easy maneuverability in tight spaces, making it ideal for confined or hard-to-reach areas.
- High-Quality Construction: Ensures reliable performance and cost-effective investment, minimizing downtime and maximizing return on your investment.
With its advanced features and robust design, the TH-900 Hydraulic Crawler Drill Rig is valuable for any drilling project.
Comparing Tianhe's Innovations with Other Manufacturers
When comparing Tianhe's innovations with other manufacturers, it becomes clear that they are at the forefront of deep hole drilling technology. Their focus on continuous improvement and customer satisfaction sets them apart, making them the preferred choice for businesses across various industries. Not only does Tianhe offer cutting-edge technology, but they also provide comprehensive training and support to ensure that their customers can maximize the potential of their drilling equipment. This dedication to customer success is unmatched in the industry and solidifies Tianhe's position as a leader in innovation.
The Ultimate Guide to Selecting the Right Tool
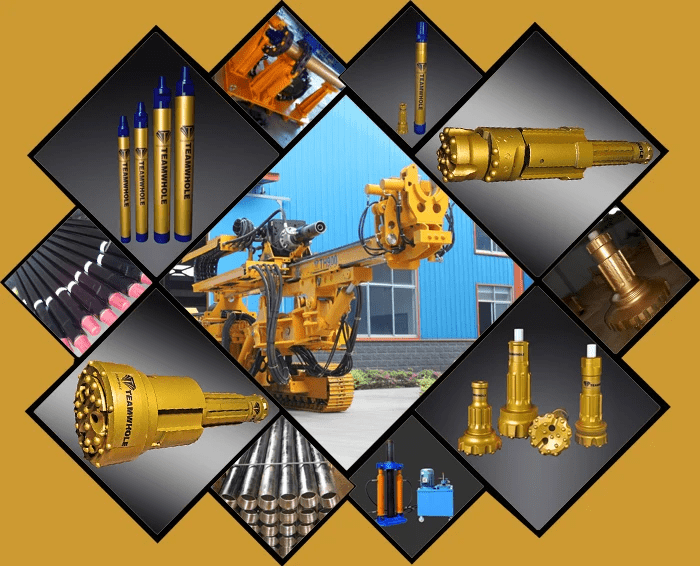
When choosing deep-hole drilling tools, it's crucial to consider factors such as the material being drilled, the depth of the hole required, and the specific application. Different tools are designed for different materials and depths, so it's important to select the right tool for the job. Additionally, considering the drill and accessories needed for efficient operation is essential for successful deep-hole drilling.
Factors to Consider When Choosing Deep Hole Drilling Tools
Deep hole drilling requires specialized equipment to achieve precise results. Here's a breakdown of key factors to consider when choosing your deep hole drilling tools:
- Material: The type of material you're drilling through significantly impacts the tool selection. Metal core drilling requires different tools than creating saw holes in concrete. Choose a tool designed for the specific material properties (hardness, brittleness, etc.) for optimal performance and tool life.
- Hole Size and Depth: The diameter and depth of the holes you need directly influence the most suitable tool. Deep hole drilling tools are designed for specific depth-to-diameter ratios. Consider the required hole dimensions to ensure your chosen tool can handle the job efficiently.
- Project Requirements: Every project has unique needs. Identify your project's specific requirements, such as hole straightness, surface finish, and production volume. Selecting a tool that meets these needs will optimize your drilling process and ensure high-quality results.
By carefully considering these factors, you can choose the most appropriate deep hole drilling tools for your project, ensuring efficiency, accuracy, and successful completion.
Tips for Maximizing Efficiency and Productivity
Deep hole drilling projects require specific strategies to maximize output. Here are some key practices to achieve optimal efficiency and productivity:
- Maintain and Sharpen Tools Regularly: High-quality, well-maintained, and properly sharpened tools are essential for efficient deep hole drilling. Regular maintenance and sharpening of saw hole bits significantly improve their performance, extend their lifespan, and reduce drilling resistance.
- Embrace Cutting-Edge Technology: Utilizing advanced boring tools equipped with the latest technology can significantly enhance precision and drilling speed. This translates to faster completion times and a more efficient overall process.
By following these practices, you can ensure your deep hole drilling projects are completed efficiently and productively, saving time and resources.
Common Mistakes to Avoid in Deep Hole Drilling
One common mistake in deep hole drilling is incorrect feed rates or drill speeds, leading to overheating or premature wear on drill bits. Another mistake is neglecting proper lubrication during drilling operations, which increases friction and reduces tool life. It's also crucial to avoid using worn-out or damaged tools, as they can compromise safety and lead to subpar results.
Remember that selecting high-performance deep hole drilling tools requires careful consideration of various factors such as material type, project requirements, maintenance practices, and avoiding common mistakes during operation. By following these guidelines, you can ensure that you select the right tool for your specific needs while maximizing efficiency and productivity in your drilling operations.
Maximizing Performance with Advanced Technology
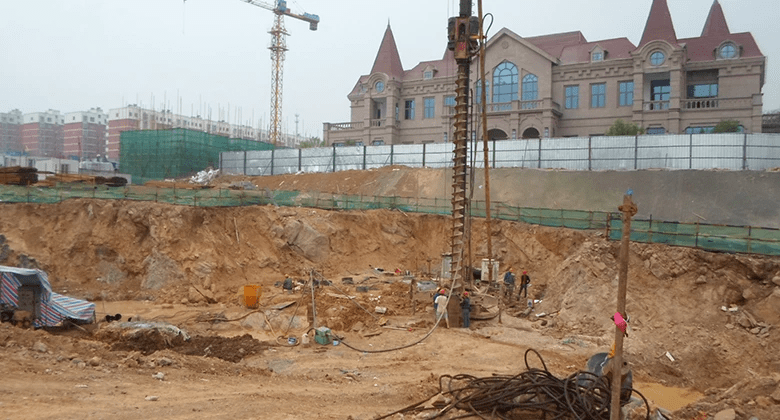
How Patented Technology Enhances Performance
When it comes to deep hole drilling tools, patented technology plays a crucial role in enhancing performance. These innovative technologies are designed to improve the efficiency, accuracy, and durability of the tools, allowing for smoother and more precise drilling operations. By integrating patented technology into the design of the tools, manufacturers can ensure that their products meet the highest standards of quality and reliability.
The Role of High Efficiency Hydraulic Rotary Impact Power Head
One of the key components contributing to the high performance of deep hole drilling tools is the hydraulic rotary impact power head. This powerful mechanism provides the necessary force and torque to efficiently drill through tough materials like concrete, rock, or metal. With its high efficiency and precision control, the hydraulic rotary impact power head is essential for achieving fast and accurate drilling results in various industrial applications.
The Benefits of a Multi-joint Steering System
Deep hole drilling requires navigating complex paths and maintaining precise core alignment. Multi-joint steering systems offer a significant advantage over traditional methods by providing several key benefits:
- Enhanced Flexibility and Maneuverability: Unlike a single-joint system, multi-joint steering allows more intricate movements within the borehole. This makes it easier to navigate around obstacles and follow curved paths.
- Improved Control and Stability: The additional articulation points provide greater control over the drill head, minimizing deflection and ensuring straighter, more accurate cores.
- Precise Core Positioning: By offering finer control during drilling, multi-joint steering systems allow operators to achieve the exact core placement required for specific project needs.
Multi-joint steering systems represent a significant advancement in deep hole drilling technology. Their ability to navigate complex geometries and ensure precise core alignment translates to improved efficiency, reduced wasted materials, and a successful drilling operation.
Now you have an informative section about maximizing performance with advanced technology in deep hole drilling tools!
Invest in Quality Tools for Long-term Success
In conclusion, it's crucial to make an informed decision when selecting high-performance deep hole drilling tools. Investing in quality tools is the key to long-term success, as they ensure efficient saw holes and drilling cores. With advanced tools, the future of deep hole drilling looks promising, offering improved productivity and precision.
Making an Informed Decision for High-performance Deep Hole Drilling
When choosing deep hole drilling tools, it's essential to consider factors such as durability, precision, and efficiency. You can ensure smooth operations and accurate project results by selecting high-performance tools like saw hole bits or drill accessories. In addition to performance, it's important to look for versatile and compatible tools with various materials and drilling conditions. This adaptability can save time and money by reducing the need for multiple tool changes or adjustments during a project. Furthermore, investing in quality tools leads to immediate benefits and sets the stage for long-term success by minimizing downtime and maintenance costs.
Investing in quality boring tools or hole drills is a smart move for long-term success in the industry. These tools offer reliability and durability and contribute to increased productivity and cost-effectiveness over time. Additionally, advanced tools can provide greater precision and accuracy, leading to higher-quality finished products. Furthermore, investing in quality tools can also reduce maintenance costs and downtime, ultimately saving money in the long run.
The future of deep hole drilling with advanced tools looks promising, with continuous innovations to enhance performance and efficiency. By embracing cutting-edge technology in deep hole drilling equipment, industries can expect improved accuracy and faster project completion.