Introduction

When it comes to down hole drilling, precision and efficiency are key. Whether it's for mining, construction, or oil and gas exploration, the success of any project hinges on effective drilling techniques. That's where Teamwhole comes in – your trusted partner for all your down the hole drilling needs.
Understanding Down Hole Drilling
Down hole drilling, also known as down the hole drilling, is a method used to create holes underground for various purposes such as mineral exploration and extraction, water well drilling, and geothermal energy production. This specialized technique involves using a down the hole drill to penetrate through different rock formations to reach the desired depth.
Down hole drilling requires precision and expertise to ensure that the holes are created accurately and efficiently. The use of advanced drilling techniques and equipment is crucial in achieving the desired results. Additionally, the process involves careful planning and analysis of the geological conditions to determine the most suitable approach for drilling. This ensures that the drilling operation is carried out with minimal disruptions and maximum productivity.
The Importance of Effective Drilling Techniques
Effective drilling techniques are the cornerstone of a successful down-the-hole well drilling project. Here are several key practices to optimize your operation:
- Selecting the Right Drill Rig: Matching the drill rig's capabilities to the project's specific needs is crucial. Factors like ground formation, desired depth, and budget all play a role in choosing the most suitable equipment.
- Optimizing Drill Bits with Advanced Treatments: Utilizing drill bits treated with advanced heat-treatment enhances their durability and performance. This translates to faster drilling and longer bit life, minimizing downtime and cost.
- Prioritizing Equipment Maintenance: Regular and thorough maintenance of your drilling equipment is essential to prevent breakdowns and delays. Even minor issues can significantly impact your project's timeline and budget.
- Investing in Skilled Personnel: Employing a team of skilled and experienced drillers who are well-versed in the latest drilling technologies is invaluable. Their expertise ensures efficient operations and maximizes the effectiveness of your drilling project.
By implementing these key techniques, you can ensure a smooth, efficient, and successful down-the-hole well drilling project.
Teamwhole: Your Go-To for Down Hole Drilling Solutions
Teamwhole is also dedicated to staying ahead of the curve regarding technological advancements in down hole drilling. Our team closely monitors industry trends and invests in cutting-edge research and development to ensure our solutions are always at the forefront of innovation. By partnering with Teamwhole, you can trust that you will have access to the latest tools and techniques for maximizing efficiency and productivity in your drilling operations.
Key Considerations for Down Hole Drilling
When it comes to down hole drilling, choosing the right drill rig is crucial for successful operations. The drill rig you select should be capable of handling the specific requirements of your project, whether it's for mining, construction, or geothermal drilling. Factors such as depth, diameter, and the type of rock formations you'll be drilling through all play a role in determining the most suitable drill rig for your needs.
Choosing the Right Drill Rig
Your choice of down hole drill rig will greatly impact the efficiency and effectiveness of your drilling operations. When selecting a drill rig, it's essential to consider factors such as mobility, power source, and drilling method. For instance, a track-mounted hydraulic drill rig might be the best option if you're working on a project requiring mobility and flexibility. On the other hand, if you're dealing with hard rock formations, a top hammer drill rig could provide the power to penetrate tough surfaces.
The Role of Down Hole Hammer Drill
The downhole hammer drill is an essential component in downhole drilling operations. This type of drill uses a hammering action to break up rock formations while drilling, providing an efficient way to advance through challenging geological conditions. By utilizing percussive force combined with rotation, downhole hammer drills can achieve faster penetration rates compared to other types of drills.
Understanding Down Hole Drilling Rig Components
Down hole drilling rigs consist of various components that work together to facilitate efficient drilling operations. Understanding these components ensures smooth and effective performance during drilling activities. Components such as the mast, rotary head, feed system, and control panel are vital in controlling and executing the drilling process.
With these key considerations in mind, you can make informed decisions about downhole drilling equipment and methods. Whether you're exploring new mineral deposits or installing geothermal wells, understanding the importance of choosing the right drill rig and utilizing downhole hammer drills will set you up for success in your drilling endeavors.
Best Practices for Efficient Drilling Operations
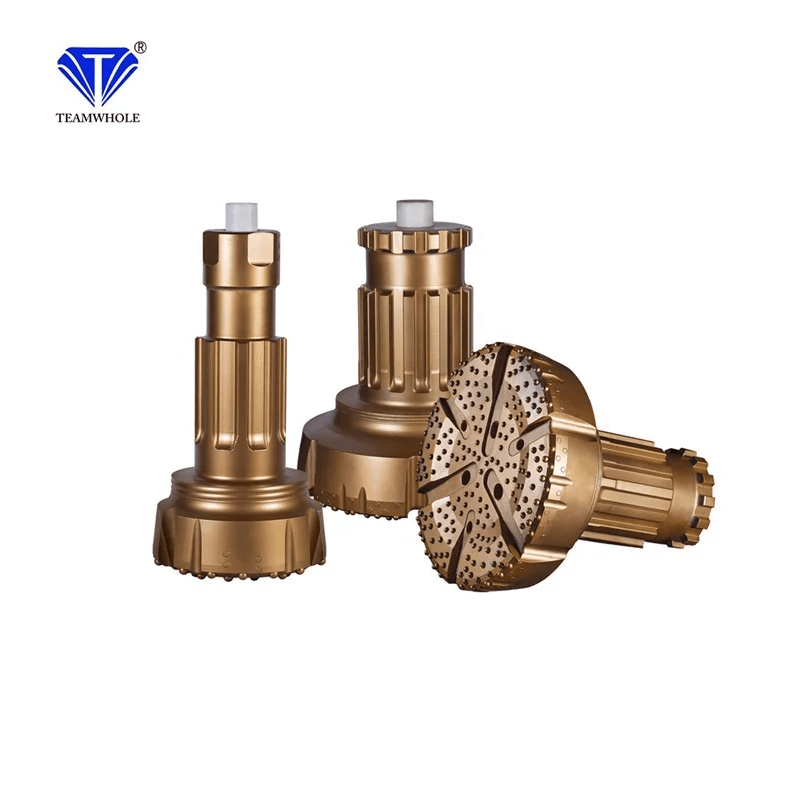
Proper Maintenance of Down Hole Drill Rig
To ensure smooth and effective down the hole drilling, regular maintenance of the down hole drill rig is crucial. This includes checking for wear and tear, lubricating moving parts, and replacing worn-out components. Keeping the drill rig in top condition can minimize downtime and maximize productivity for your drilling operations.
Utilizing Advanced Heat-Treatment for DTH Bits
When it comes to downhole drilling, the quality of your DTH bits can significantly affect performance. Utilizing advanced heat-treatment techniques can enhance their durability and resistance to wear. This ensures that your bits maintain their sharpness and cutting efficiency even in challenging rock formations, ultimately leading to more efficient drilling operations.
Maximizing Efficiency with Different Bit Head Face Designs
Another key aspect of efficient down the hole drilling is maximizing the efficiency of your bit head face designs. You can optimize penetration rates and overall performance by choosing the right design based on the specific rock formations you are drilling through. Whether it's a convex, concave, or flat face design, selecting the most suitable option can significantly enhance your drilling efficiency.
Enhancing Performance with Quality Drill Bits

When it comes to down the hole drilling, the significance of alloy steel in DTH bits cannot be overstated. Alloy steel offers exceptional strength and durability, making it the ideal material for withstanding the rigors of drilling through tough rock formations. This ensures that the DTH bits are able to maintain their cutting edge and deliver consistent performance throughout the drilling process.
The Significance of Alloy Steel in DTH Bits
Alloy steel is specifically engineered to withstand extreme pressure and heat, making it perfect for down hole drilling operations. Its superior hardness and toughness allow DTH bits to maintain their sharpness and integrity even in the most challenging drilling conditions. This ensures efficient penetration and minimizes downtime for bit replacements, ultimately leading to cost savings and improved productivity.
In addition to its durability, alloy steel also offers excellent corrosion resistance, which is crucial for drilling in various geological formations. This feature ensures that DTH bits remain in optimal condition even when exposed to harsh chemical environments, prolonging their lifespan and reducing the frequency of replacements. As a result, drilling operations can be carried out with minimal interruptions, leading to increased efficiency and cost-effectiveness.
Customizing Carbide Shapes for Specific Rock Formations
In down hole well drilling, customizing carbide shapes in DTH bits is crucial for optimizing performance in different rock formations. By tailoring the carbide shape to match specific geological conditions, such as hard or abrasive rock, DTH bits can achieve maximum efficiency and longevity. This customization allows for precise control over drilling parameters, resulting in faster penetration rates and reduced wear on equipment.
Teamwhole offers a diverse line of DTH bits specifically designed to address the varying needs of different rock formations. From soft to hard rock, our range of DTH bits can be customized with carbide shapes tailored to the specific geological conditions encountered during drilling. This ensures that our customers can achieve optimal performance and longevity in their drilling operations, regardless of the type of rock they work with. With Teamwhole's customized DTH bits, drillers can have confidence in their ability to tackle any rock formation with maximum efficiency.
Teamwhole's Diverse Line of DTH Bits
Teamwhole offers a diverse line of high-quality DTH bits designed to meet the unique needs of various down hole drilling applications. From standard designs to specialized configurations for specific geological conditions, Teamwhole's comprehensive range of DTH bits ensures that customers can find the perfect solution for their drilling requirements. With a focus on innovation and reliability, Teamwhole sets the standard for excellence in down hole drill bit technology.
In addition to offering a diverse range of DTH bits, Teamwhole provides expert technical support and guidance to help customers select the most suitable drill bit for their specific drilling needs. With a team of experienced engineers and industry professionals, Teamwhole is committed to ensuring that customers can access the knowledge and expertise they need to maximize drilling efficiency and productivity. By offering comprehensive support alongside its high-quality products, Teamwhole stands out as a trusted partner in the down hole drilling industry.
Overcoming Challenges in Down Hole Drilling
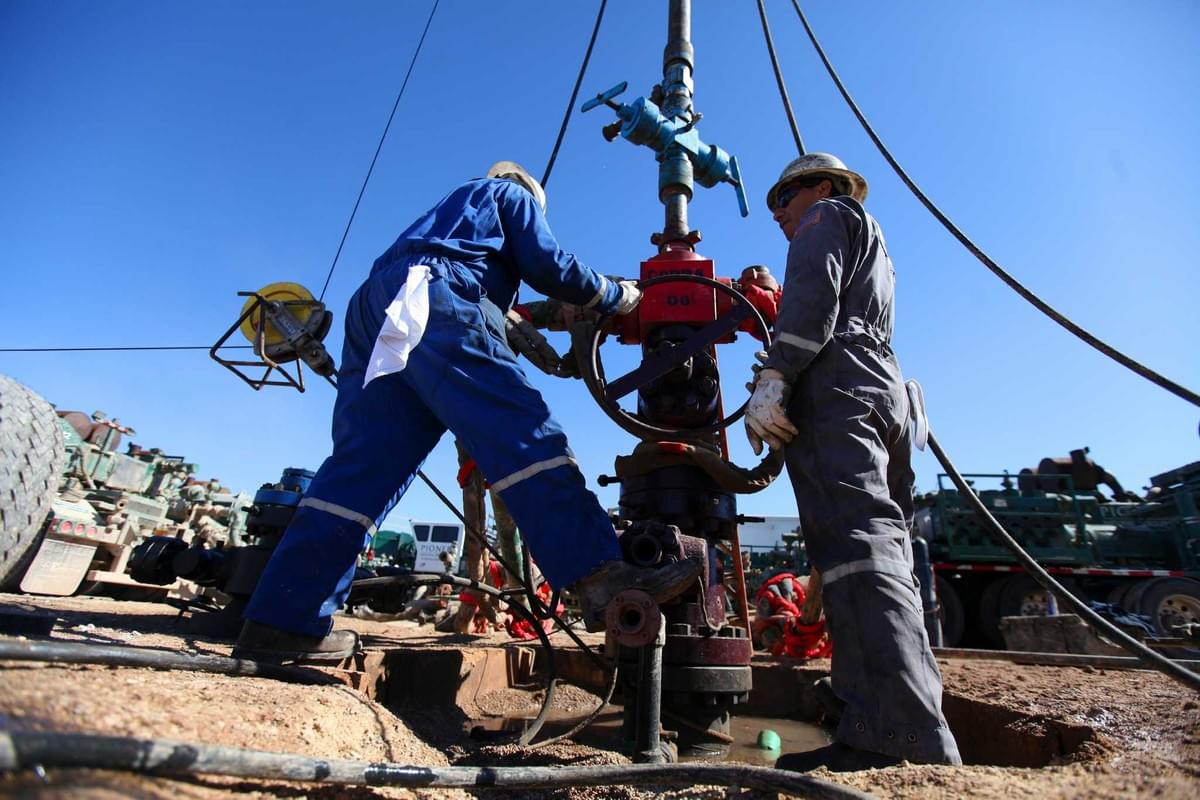
When it comes to down hole drilling, wear and fatigue are common challenges that can impact efficiency and productivity. Constant friction and pressure can lead to wear on the drill rig components, affecting performance and longevity. However, these issues can be addressed with proper maintenance and regular inspections to ensure smooth operations and extended equipment lifespan.
Addressing Wear and Fatigue in Drilling Operations
Regular inspection of the down hole drill rig components is crucial to identify signs of wear and fatigue early on. By addressing any issues promptly through repairs or replacements, you can prevent costly downtime and maintain optimal drilling performance. Additionally, utilizing high-quality materials for drill rig components can help minimize wear and fatigue, ensuring durability even in the most demanding drilling conditions.
Adapting to Various Rock Formations
Adapting to various rock formations is another challenge in down the hole drilling. Different geological formations require different drilling techniques and tools to penetrate the rock layers effectively. Understanding the specific characteristics of each formation is essential for selecting the right drill rig and bit design to achieve efficient drilling results without compromising equipment integrity.
Teamwhole's Extreme Protection Guarantee
Teamwhole understands the challenges of downhole well drilling and offers an Extreme Protection Guarantee for its products. Focusing on durability, reliability, and performance, Teamwhole's downhole drill rigs, DTH bits, and other drilling solutions are engineered to withstand extreme conditions while delivering exceptional results. This guarantee provides peace of mind for operators facing challenging drilling environments.
Partnering with Teamwhole means accessing reliable solutions that address wear and fatigue in drilling operations, adapt to various rock formations, and provide extreme protection against challenging conditions in down hole drilling.
Partner with Teamwhole for Superior DTH Solutions
In conclusion, mastering down hole drilling is crucial for successful mining, construction, and geothermal projects. With the advancements in down the hole drilling technology, we can expect faster and more efficient drilling processes. By partnering with Teamwhole for superior DTH solutions, you can optimize your down hole drilling operations for maximum productivity and success.
Achieving Success with Effective Down Hole Drilling
Achieving success with effective down hole drilling requires a deep understanding of the drilling process and the right equipment. It's not just about getting the job done; it's about doing it efficiently to save time and resources. With the right techniques and equipment like a down hole drill rig, you can achieve success in your drilling operations.
The Future of Down the Hole Drilling Technology
The future of down the hole drilling technology looks promising with continuous innovations aimed at improving efficiency and reducing environmental impact. As technology advances, we can expect to see more powerful and precise down hole hammer drills that make drilling faster and more accurate than ever before.
Partnering with Teamwhole for superior DTH solutions means gaining access to top-notch equipment and expertise in down hole well drilling. With their diverse DTH bits and extreme protection guarantee, you can trust that your drilling operations are in good hands.
Remember, when it comes to down hole drilling, choosing the right partner is just as important as choosing the right equipment. Teamwhole offers comprehensive solutions for all your down hole drilling needs. Contact us today to learn how we can elevate your drilling operations to new heights!